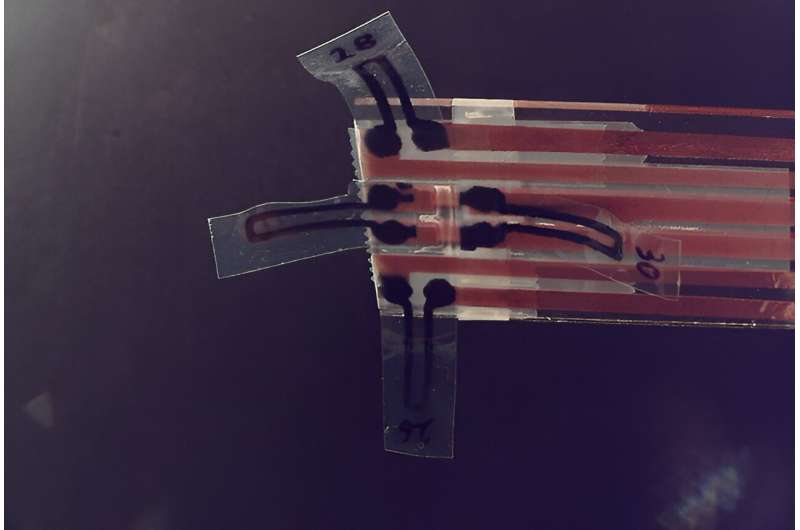
Eindhoven researchers have developed a soft robotic “hand” made from liquid crystals and graphene that could be used to design future surgical robots. The new work has just been published in the journal ACS Applied Materials & Interfaces.
In our future hospitals, soft robots might be used as surgical robots. But before that can happen, researchers need to figure out how to precisely control and move these deformable robots. Added to that, many current soft robots contain metals, which means that their use in water-rich environments—like the human body—is rather limited.
TU/e researchers led by Ph.D. candidate Laura van Hazendonk, Zafeiris Khalil (as part of his master’s research), Michael Debije, and Heiner Friedrich have designed a soft robotic hand or gripper made from graphene and liquid crystals (both organic materials). This opens the possibilities for such a device to be potentially and safely used in surgeries in the future.
Robots have an enormous influence on our world. For instance, in industry, robots build automobiles and televisions. In hospitals, robots—such as the da Vinci robotic surgical system—assist surgeons and allows for minimally invasive operations. And some of us even have robots to do our vacuum cleaning at home.
“Society has become dependent on robots, and we’re coming up with new ways to use them,” says Van Hazendonk, Ph.D. researcher in the Department of Chemical Engineering and Chemistry. “But in devising new ways to use them, we need to think about using different types of materials to make them.”
Thinking soft
The different materials that Van Hazendonk is referring to are fluids, gels, and elastic materials—which are all easily deformable. “Typically, robots are made from metals, which are rigid and hard. But in certain applications, robots made from hard and rigid materials limit the performance of the robot,” says Van Hazendonk. “The solution is to think soft.”
In soft robotics, the goal is to make robots from materials like fluids or gels that can deform in certain situations and then can act like robots made from traditional rigid and hard materials.
One area where soft robots look set to have a major impact is in surgical procedures. Van Hazendonk adds, “For a surgeon, many operations can be complex and delicate, and therefore require precise dexterity on the part of the surgeon. Sometimes this just isn’t possible, and they turn to robots.
“But rigid robots may not be able to access some areas with ease either. That’s where soft robots can come to the fore, and our goal was to offer the potential new helping hand for use in clamping and suturing used devices in surgeries, for example.”
Turning to Nobel materials
For their research, Van Hazendonk and her colleagues opted to use a different type of deformable material—liquid crystals—along with graphene to make a soft gripper device or “hand” with four controllable and deformable “fingers.”
Intriguingly, both liquid crystals and graphene are directly or indirectly connected to Nobel Prizes in Physics over the last 30 years or so. Back in 1991, Pierre-Gilles de Gennes won the prize for his work on order in complex matter, such as liquid crystals. And in 2010, Andre Geim and Konstantin Novoselov won the prize for their work on graphene—the super-strong material that is also transparent and an effective conductor of electricity and heat.
“A liquid crystal behaves as a liquid or a solid depending on how it is excited or perturbed. When it flows, it acts like a liquid. But in special situations, the molecules in the liquid can arrange themselves to create a regular pattern or structure, such as a crystal you would see in a solid material under a powerful microscope,” explains Van Hazendonk. “The ability for liquid crystal materials to act like this is perfect when it comes to making soft robots.”
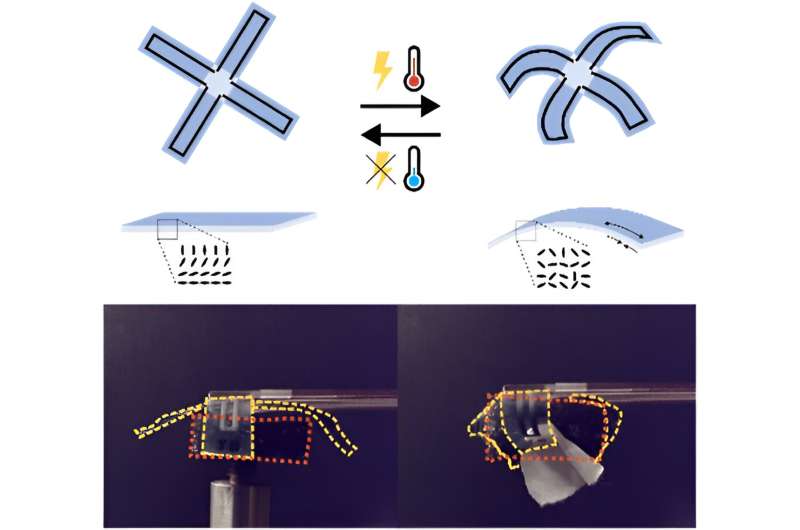
Actuator challenge
With the materials selected, the researchers set out to design and make an actuator. “Actuators control and regulate motion in robotic systems. Usually, the actuator responds or moves when supplied with electricity, air, or a fluid,” says Van Hazendonk. “In our work, we turned to something else to drive liquid-crystal network (LCN) actuators.”
The researchers designed a gripper device with four ‘fingers’ controlled using LCN actuators that are deformed thanks to the effect of heat on graphene-based heating elements or tracks in the fingers of gripper or ‘hand.”
Bending of the fingers
“When electrical current passes through the black graphene tracks, the tracks heat up and then the heat from the tracks changes the molecular structure of the liquid crystal fingers and some of the molecules go from being ordered to disordered. This leads to bending of the fingers,” says Van Hazendonk. “Once the electrical current is switched off, the heat is lost, and the gripper returns to its initial state.”
One of the biggest challenges for the researchers related to the graphene heating elements as highlighted by Heiner Friedrich, assistant professor at the Department of Chemical Engineering and Chemistry.
“We needed to make sure that they would heat to the right temperature to change the liquid crystal layer, and we needed to make sure that this could be done at safe voltages. Initially, the graphene elements didn’t reach the right temperatures at safe voltages, or they would overheat and burn the device,” says Friedrich. “This and many other important problems were solved by Zafeiris Khalil during his MSc thesis.”
The researchers didn’t let this problem deter them, and in the end, they designed an actuator that can operate without any issues at voltages less than 15 volts. And in terms of performance, the grippers can lift small objects with a mass between 70 and 100 milligrams. “This might not sound like a lot, but in medical applications such as surgery, this can be useful for the exact and miniscule movement of tiny tools, implants, or biological tissue,” says Van Hazendonk.
For Van Hazendonk—who combines her Ph.D. research with being a member of the provincial parliament of Noord-Brabant (Provinciale Staten)—this research has been eye-opening for her.
She says, “I love how this work combines a useful and tangible application. The gripper device is based on fundamental technologies, but the actuator itself could form the basis for a suite of robots for use in biomedical or surgical applications in the future.”
And, in the future, Van Hazendonk and her colleagues have some interesting plans. She concludes, “We want to make a fully printed robot by figuring out a way to 3D-print the liquid-crystal layer. For our gripper, we made the layer by casting materials in a mold. Other researchers in the group of Michael Debije have shown that liquid crystals can be printed. For this gripper, we have printed the graphene layer, so it would be cool to have a fully printed device.”
More information:
Laura S. van Hazendonk et al, Hot Fingers: Individually Addressable Graphene-Heater Actuated Liquid Crystal Grippers, ACS Applied Materials & Interfaces (2024). DOI: 10.1021/acsami.4c06130
Citation:
New soft robotic gripper designed with graphene and liquid crystals (2024, June 18)
retrieved 24 June 2024
from https://techxplore.com/news/2024-06-soft-robotic-gripper-graphene-liquid.html
This document is subject to copyright. Apart from any fair dealing for the purpose of private study or research, no
part may be reproduced without the written permission. The content is provided for information purposes only.